Inventory is a crucial asset for any company that sells physical products, and how it is managed has a significant impact on business profitability. In order to successfully complete orders, businesses need an inventory management system that offers them a clear picture of how many items are available at each location in real-time. Not having reliable inventory records can result in poor order fill rates, delivery holdups, inflated inventory expenses, and more.
Thanks to inventory cycle counts, businesses can easily achieve and maintain accurate inventory lists, enhance their operations, and save time and money. That’s why it is so important to conduct inventory counts on a regular basis.
In this post, we’re providing an answer to the question “What is cycle count in inventory?”, the benefits of conducting regular inventory cycle counts, and how inventory management software can help you streamline the process.
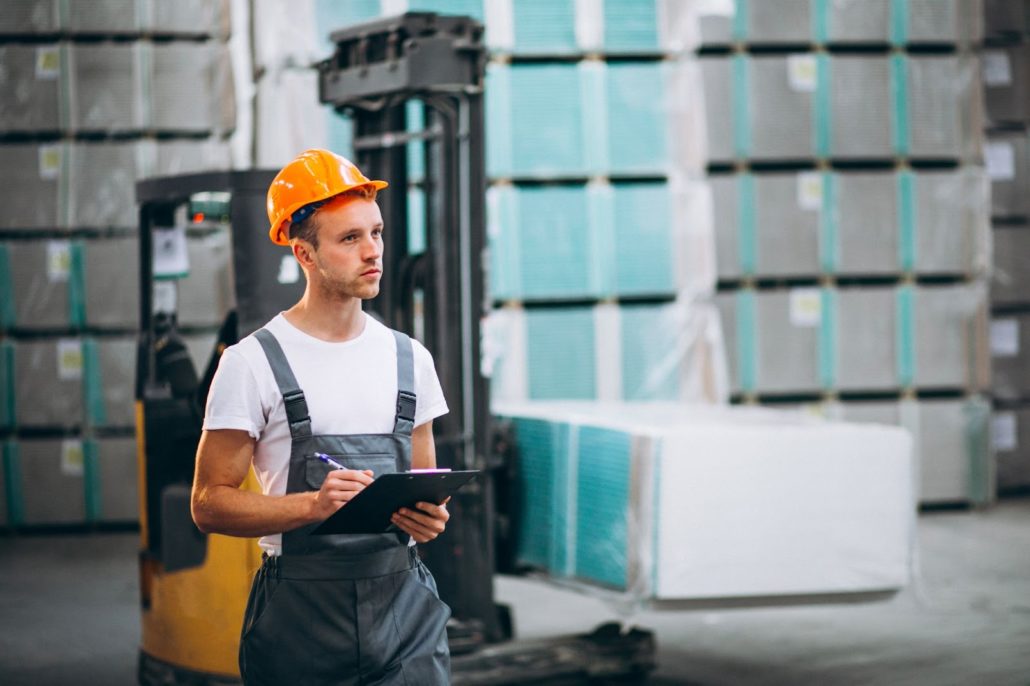
Image by sanivpetro on Freepik
What is Cycle Count in Inventory
An inventory cycle count is a method of counting inventory that involves rotating through predetermined, specified portions of stock on a regular basis. The schedule specifies the precise time each inventory item will be counted. You can arrange daily or weekly inventory counts of specific categories of items so you don’t have to count your entire inventory all at once.
Difference Between Cycle Counting and Physical Counting
Physical inventory counts every item of inventory at once, typically annually or semi-annually. Cycle counting, on the other hand, is the process of counting smaller, pre-selected portions of inventory multiple times throughout the year, sometimes even daily.
Performing physical inventory is a good option for businesses with little inventory. Schedule and conduct an annual physical inventory count if you can simply count your stock without closing and inconveniencing your customers. Many businesses conduct cycle counting in addition to an annual physical count in order to get a solid understanding of their inventory.
Why is Inventory Cycle Count Important?
Cycle counting has become a popular inventory management technique for businesses across various industries because it doesn’t need businesses to stop all daily operations and do a thorough physical inventory count at once. Among the most significant advantages are:
- Reduced required safety stock
- Less obsolete inventory and fewer inventory write-offs
- Reduced overhead expenses and employee overtime expenses
- Increased order fulfillment rates
- Time savings
- More accurate inventory assessments
- Reduced errors
- Improved customer service
- Improved sales
- More time between physical counts
- Increased productivity and improved business operation
- Timely detection of thefts
Types of Inventory Cycle Counting
There are numerous types of inventory cycle counting techniques that can be tailored to meet various business requirements. Among the strategies used the most frequently are:
Random sample cycle count
This method is a great choice if your products are similar. With random sample cycle counting, you can select a random sample of the products to count throughout each cycle count. The benefit is less downtime for your warehouse or retail location since random cycle counts can take place during regular business hours. There are two methods for counting random samples:
- Constant population counting. With this method, the same number of products is counted every time. Because the products are selected at random, there is always a risk that some of them might not be counted at all while others might be counted repeatedly.
- Diminished population counting. Products that have already been counted are not included in subsequent cycle counts until all inventory has been counted. The procedure then starts over.
Control group cycle count
With this method, a small number of inventory items are audited repeatedly over a short period of time. The control group method works well when a business is new to cycle counting. By regularly counting a small group of representative objects, managers can find and fix flaws in the counting method. The procedure can be used on other product groups once it has been refined and no faults are reported.
ABC analysis
One of the easiest and most widely used cycle count techniques is the ABC analysis cycle count. It’s based on the 80/20 Pareto rule, which states that 20% of your items account for 80% of your results. The top 20% of the most valuable items should make up the A group, followed by the middle 30% of products with medium value, and the bottom 50% of the least valued item. The highest priority items, those marked with an A, are counted most often, whereas the items in category C are the least important and are counted least frequently.
How to Do Cycle Counting
Now that you have learned about the different types of inventory cycle counts, let’s look at how to conduct your inventory cycle counts effectively.
1. Go through your inventory records
Starting with an accurate database is important. Review all data entries for inventory transactions and make sure to correct any discrepancies.
2. Start counting
Review the inventory amounts, locations, and descriptions from your inventory records and compare them to what is actually present in your stockroom, warehouse, or sales floor.
3. Investigate and reconcile any differences
Identify the inventory discrepancies discovered during cycle counts and resolve them with your inventory management employees and in your system.
4. Alter your procedures if necessary
If the same problems are occurring frequently, you could need to fix the holes in your strategy or even establish an entirely new inventory counting procedure.
5. Adjust your inventory records
After cycle counts are finished, be sure to include a stage in your process to update your inventory management system to match your physical inventory.
6. Repeat the cycle counting process
The cycle counting process should be repeated on a regular basis. You can opt to do it daily, weekly, monthly, or quarterly depending on your business. The more often you perform inventory cycle counts, the more accurate they will be.
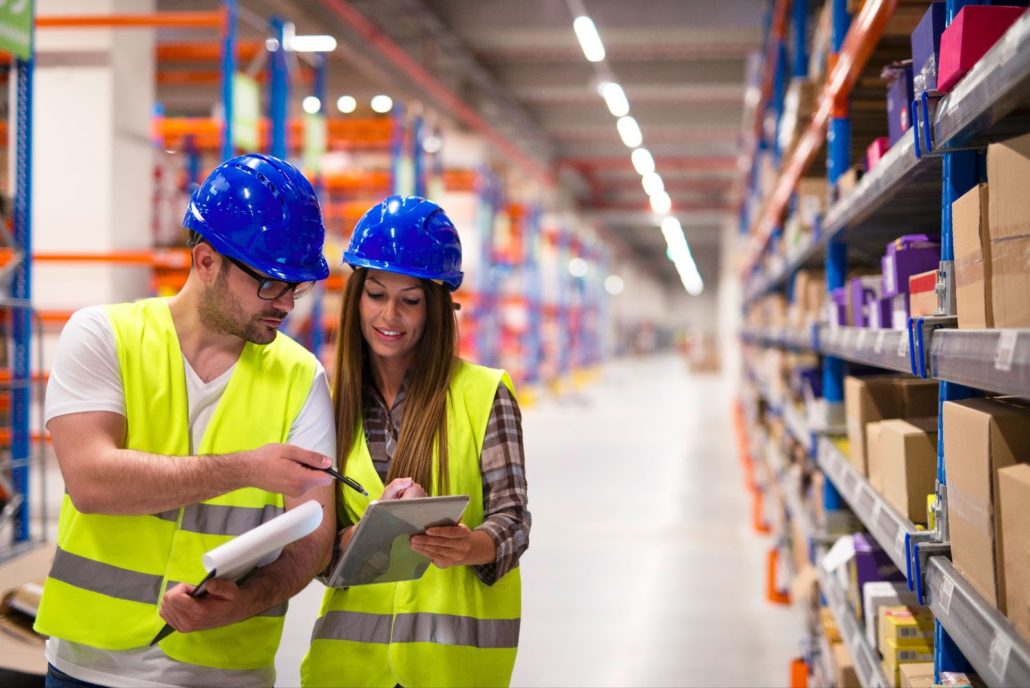
Image by aleksandarlittlewolf on Freepik
Best Practices for Cycle Count Inventory
The following best practices will help you launch, manage, and improve your inventory cycle count process:
Plan beforehand. It’s crucial to plan out your product counts at the very beginning so that you can make sure that every item is inventoried at least once every three months.
Close out everything before the beginning of the count. Make sure that any open receiving, WIP transaction, and shipping for the products that have been chosen for the cycle count are closed before beginning one.
Start the inventory cycle counts early in a shift, either before your operations have cycled up for the day or late in the shift when things have settled down. This will cause less disturbance and movement, which makes the counts easier.
Double-check your counts and deal with issues that cause discrepancies. In order to get accurate results, make sure that at least two people count the same item separately. Compare the findings, and if you notice any discrepancies, look into what might be causing them.
Track your progress over time. It’s critical to monitor your inventory cycle counts over time and look for patterns so that you can identify the systems that are not functioning and make the necessary adjustments.
Document your cycle count process. Make a clear, concise document that explains how your inventory cycle counting works. The document should be simple enough so that every new employee can understand it, but also detailed enough for existing staff members to understand the procedures for handling issues.
Use inventory management software. Even though you can use spreadsheets to count and track your inventory, inventory management software that uses barcodes or QR codes is a much better option because it can streamline the procedure and significantly improve the level of accuracy of your counts. Rather than manually updating your inventory at regularly scheduled times, inventory management solutions like ApparelMagic record purchases and outbound orders and all associated costs in real-time. More accurate metrics mean fewer mistakes that can unbalance your inventory levels.
The Bottom Line
Cycle counting makes inventory management and inventory reconciliation easier because you can concentrate on smaller product portions, spend less time counting, avoid closing your store’s doors and miss out on sales.
ApparelMagic can help you improve inventory tracking and increase inventory accuracy. Accurate inventory tracking from the time you receive a product to the moment you deliver it, means lower inventory costs, decreased risk of error, higher customer satisfaction rates, and more efficient overall operations.