Garment manufacturing is a highly competitive industry, and staying ahead often means finding innovative ways to reduce costs without compromising quality.
Whether you’re a small-scale producer or a large factory owner, cost optimization is critical for increasing profitability, maintaining competitiveness, and achieving sustainable growth.
Let’s explore proven strategies for cutting costs while embracing efficiency and sustainability.
Understanding Cost Optimization in Garment Manufacturing
Cost optimization involves streamlining processes, reducing waste, and managing resources wisely to enhance profitability. In the garment sector, where margins are often tight, cost optimization is essential for staying competitive in the global market.
Here are some benefits of cost optimization in this area:
- Improved competitiveness: Lower production costs enable you to offer competitive prices, attracting more clients.
- Increased profitability: Efficient use of resources directly impacts the bottom line, allowing you to reinvest in growth.
- Sustainable growth: Adopting cost-effective, eco-friendly practices positions your brand as both responsible and forward-thinking.
Sustainability plays a dual role here: reducing costs and appealing to eco-conscious consumers. Additionally, efficient production management ensures smooth operations, fewer delays, and better product quality, ultimately leading to cost savings.
Key Areas to Optimize in Garment Manufacturing
To achieve meaningful reductions in production costs, manufacturers must focus on materials, labor, and overhead expenses. These components form the backbone of garment production and represent significant opportunities for efficiency improvements.
Material Cost Optimization
Materials are often the most significant expense in garment manufacturing, accounting for nearly half of total production costs. Optimizing this area requires careful management and smart technology integration. Digital tools and software can track fabric usage with precision, minimizing waste and ensuring optimal utilization during the cutting process. Automated cutting machines, for instance, not only save time but also reduce errors, ensuring that every piece of fabric is used effectively.
Another avenue is the adoption of eco-friendly materials, such as recycled or organic fabrics. While these options might involve higher upfront costs, they often lead to long-term savings by reducing waste and enhancing brand value. Consumers increasingly favor sustainable products, making these investments both cost-effective and reputation-enhancing. Coupled with effective inventory management practices, such as aligning fabric orders with production schedules, manufacturers can avoid overstocking and lower carrying costs.
Labor Cost Strategies
Labor represents another substantial component of production costs, but targeted strategies can optimize manpower and improve productivity. Training employees across multiple roles fosters flexibility and reduces downtime during peak production periods. This approach ensures workers can seamlessly transition between tasks, keeping operations smooth and efficient.
Lean manufacturing principles also play a pivotal role in labor cost optimization. By eliminating waste and streamlining workflows, manufacturers can achieve higher output with fewer resources. Regular process studies further refine operations, identifying bottlenecks or inefficiencies that might otherwise go unnoticed. These combined efforts reduce labor expenses and create a more productive and engaged workforce.
Reducing Overhead Expenses
Overhead costs, including energy consumption, rent, and maintenance, significantly influence production expenses. Implementing energy-efficient technologies, such as LED lighting and energy-saving equipment, is one effective way to reduce utility bills. Renewable energy sources, like solar panels, offer additional long-term savings while supporting sustainability goals.
Periodic reviews of overhead expenses are equally important. Renegotiating contracts with suppliers, optimizing production facilities, or consolidating operations can all contribute to substantial cost reductions. A strategic approach to overhead management not only lowers costs but also reduces the environmental footprint of garment manufacturing operations, aligning the business with modern consumer expectations.
Sustainability as a Long-Term Cost Strategy
As mentioned, sustainability is no longer an optional consideration in garment manufacturing—it is a necessity for long-term success. Beyond its environmental benefits, sustainability offers substantial cost savings. For instance, implementing energy-efficient technologies and renewable energy sources can lower operational expenses over time. IoT-enabled smart technologies allow manufacturers to monitor and optimize energy usage, further reducing costs.
Eco-friendly practices also extend beyond energy consumption. Many manufacturers are now investing in water recycling systems for dyeing processes or switching to biodegradable packaging. These measures not only lower production costs but also align with growing consumer demand for responsible manufacturing practices.
Optimizing the Supply Chain for Cost-Effective Garment Manufacturing
An optimized supply chain is the backbone of efficient garment manufacturing, directly impacting production costs and operational performance. Managing logistics, transportation, and supplier relationships effectively can lead to substantial savings while ensuring a steady flow of materials and timely deliveries.
Cost-Efficient Transportation
Transportation is a significant cost driver in garment manufacturing, but choosing the right methods can make a difference. For high-volume shipments, sea transport offers a cost-effective solution with lower fuel expenses compared to air freight. Similarly, rail transport is ideal for moving heavy goods over long distances, providing a balance of affordability and reliability with fewer delays than road freight.
For manufacturers seeking flexibility, multimodal transport—a combination of sea, rail, and road—provides an efficient way to reduce costs while maintaining delivery speed. This approach allows businesses to optimize their logistics strategy based on the specific needs of each shipment, whether it’s prioritizing cost or timeliness.
Enhancing Supplier Relationships
Supplier management is another cornerstone of an optimized supply chain. Building strong, collaborative relationships with suppliers unlocks opportunities for better pricing and consistent material quality. By maintaining open communication and conducting regular performance evaluations, manufacturers can ensure suppliers meet production standards and timelines.
These relationships also foster trust, enabling manufacturers to negotiate more favorable terms, such as bulk discounts or priority delivery schedules. A well-managed supplier network minimizes risks of material shortages or delays, ensuring seamless operations and reducing unexpected costs.
Streamlining Supply Chain Logistics
Efficient supply chain logistics involve more than just transportation and supplier management. Integrating advanced tools, such as real-time tracking systems and data analytics, provides visibility into every stage of the supply chain. This transparency allows manufacturers to identify bottlenecks, streamline workflows, and make informed decisions that reduce waste and costs.
Incorporating strategic transportation modes and fostering robust supplier relationships is essential for optimizing the supply chain in garment manufacturing. By doing so, businesses can lower logistics expenses, enhance operational efficiency, and maintain a competitive edge in the market.
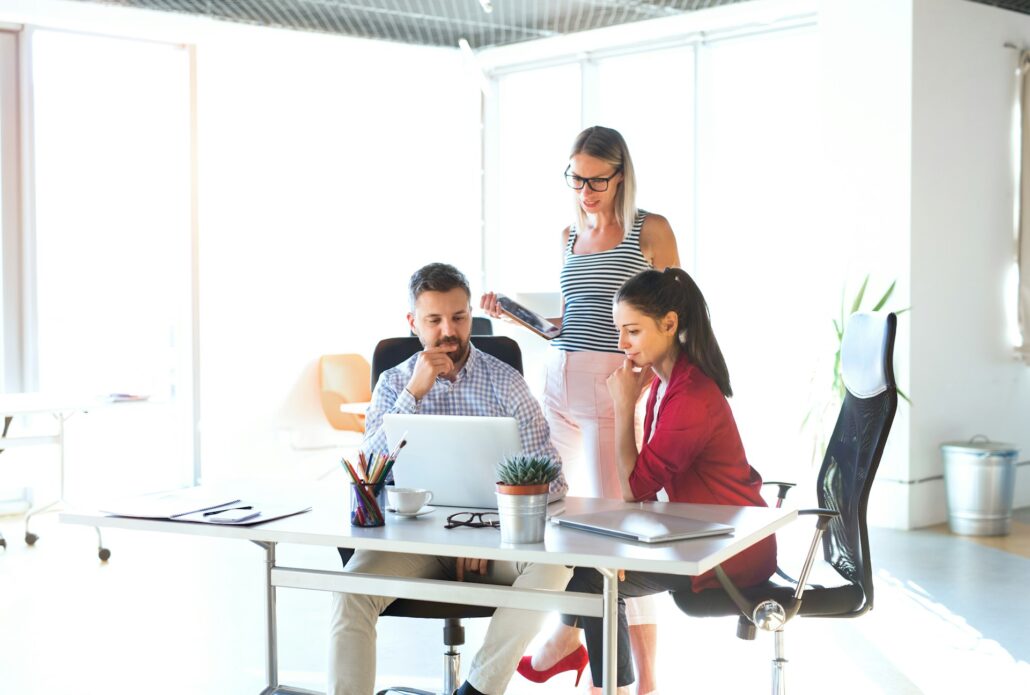
Leveraging Technology: How ApparelMagic Simplifies Garment Manufacturing
Optimizing garment manufacturing costs requires the right tools, and ApparelMagic offers an all-in-one ERP solution tailored to the unique needs of the apparel industry. By integrating core functionalities such as inventory management, production planning, supply chain coordination, and financial oversight, ApparelMagic streamlines operations and reduces inefficiencies across the board.
With its robust inventory management system, ApparelMagic enables manufacturers to track raw materials and finished goods in real time, reducing carrying costs and preventing overstocking. This level of control supports just-in-time inventory practices, ensuring materials align perfectly with production schedules.
In supply chain optimization, ApparelMagic fosters supplier collaboration through centralized communication and tracking tools, making it easier to negotiate terms, monitor performance, and ensure timely material deliveries. For logistics, the system integrates seamlessly with shipping providers, offering real-time updates on order statuses and enabling businesses to identify the most cost-effective transportation methods.
ApparelMagic also enhances production planning by integrating tools for design management, materials tracking, and product lifecycle management (PLM). This functionality ensures accurate costing, efficient resource allocation, and reduced development time, helping businesses bring products to market faster and at a lower cost.
Moreover, the platform automates repetitive tasks, such as order processing and invoicing, freeing up valuable time for strategic decision-making. Its comprehensive financial management tools consolidate data across departments, providing clear insights into cost structures and profitability.
If you too want to enjoy the benefits of ApparelMagic, schedule your demo now and start enjoying the benefits.
Conclusion
Optimizing costs in garment manufacturing is crucial for enhancing profitability and maintaining competitiveness. By focusing on key areas such as material, labor, and overhead costs, and adopting efficient production techniques, you can achieve substantial cost savings.
Implementing sustainable practices and advanced technologies further enhances efficiency and ensures long-term growth. Embrace these strategies to transform your garment manufacturing process and achieve lasting success.